In den letzten Jahren hat sich die Metallbearbeitung durch den Einsatz von Lasertechnologie erheblich weiterentwickelt. Der fokussierte Laserstrahl schmilzt das Metall punktgenau und ermöglicht so präzises Schneiden und Schweißen. Besonders leistungsfähige Festkörperlaser haben die Bearbeitung von größeren Materialdicken revolutioniert, die zuvor als nicht realisierbar galten. Diese Technik ist beim Schneiden von Blechen inzwischen unverzichtbar und bietet durch ihre Flexibilität zahlreiche neue Anwendungsmöglichkeiten. Selbst komplexe Geometrien können wirtschaftlich auch in kleinen Stückzahlen gefertigt werden.
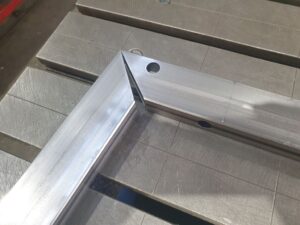
Seit vielen Jahren schon findet bei uns die Lasertechnik auch in der Bearbeitung von Rohren Anwendung. Durch den Lasereinsatz lassen sich Rohre dreidimensional bearbeiten, wodurch eine Vielzahl an Geometrien erzeugt werden kann. Der Bearbeitungsprozess beginnt mit dem Einlegen eines Rohres in die Laserschneidmaschine. Üblicherweise beträgt die Standardlänge der Rohre sechs Meter, ein Format, das die meisten Maschinen problemlos verarbeiten können. Rohrlaser sind mit Rund-, Quadrat- und Rechteckrohren kompatibel und lassen sich mit angepassten Spannmitteln auch für Sonderprofile wie U-Profile einsetzen.
Neben der flexiblen Geometriegestaltung bieten Rohrlaser weitere Vorteile: Sie ermöglichen die Integration von Features, die das Produkt verbessern sowie nachfolgende Bearbeitungsschritte optimieren und vereinfachen.
Vorreiter der Rohrlasertechnik
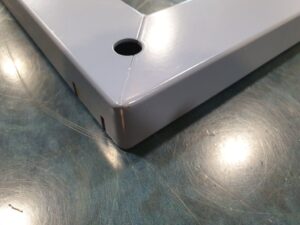
Wir bei Metallbau Nick gehören quasi zu den Pionieren der Rohrlasertechnologie. Bereits 2001 wurde der erste Rohrlaser bei uns in Lampertheim angeschafft und in die Serienfertigung integriert. Gerade bei komplexen Rohrgeometrien konnte das Unternehmen frühzeitig von den Vorteilen profitieren. Ein entscheidender Faktor für den erfolgreichen Einsatz der Rohrlasertechnik ist die direkte Integration der Schneidtechnik in die Konstruktion. Dennoch zeigt sich häufig, dass viele Konstruktionsabteilungen die Potenziale dieser Technologie nicht voll ausschöpfen.
Als erfahrener Zulieferer sehen wir uns daher in der Pflicht und als eine zentrale Aufgabe, Kunden über die Vorteile einer rohrlasergerechten Konstruktion zu informieren.

Ein anschauliches Beispiel für das Optimierungspotenzial ist die Herstellung eines L-förmigen Bauteils aus einem Rohrstück. Traditionell würde dieses aus zwei auf Gehrung geschnittenen Bauteilen gefertigt und anschließend zusammengeschweißt. Mit der Rohrlasertechnik kann hingegen ein sogenanntes Knickschnitt-Bauteil produziert werden. Dieses verfügt über Positionierhilfen und wird lediglich geknickt, wodurch sich der Schweißaufwand erheblich reduziert. Da das Bauteil aus einem Stück gefertigt wird, bleibt die Stabilität erhalten, während die Produktionszeit um rund 49 Prozent und die Kosten um circa 31 Prozent gesenkt werden können.
Knickschnitte – effiziente Alternative zur Gehrungsschnitt-Technik
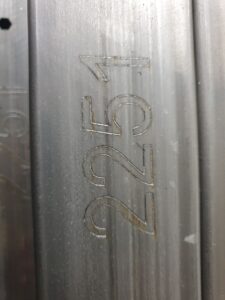
Viele Anwendungen setzen nach wie vor auf die klassische Gehrungsschnitt-Technik. Dabei werden Rohre zunächst in einzelne Segmente gesägt und anschließend zu einem Rahmen verschweißt. Dies erfordert eine präzise Positionierung und zusätzliche Bearbeitungsschritte. Der Rohrlaser ermöglicht hier eine effizientere Alternative: Statt vier Einzelteile zusammenzusetzen, wird der Rahmen bereits in einem Stück gefertigt. Spezifische Ausschnitte in der Rohrstruktur erlauben es, das Bauteil an diesen Stellen um 90° zu knicken. Durch diese Technik entfällt die aufwendige Positionierung der einzelnen Teile, da das Werkstück eine durchgängige Struktur beibehält. Zudem kann oft auf eine vollständige Rundum-Schweißung verzichtet werden, da eine einfache Kehlnaht ausreicht.
Ein weiterer Vorteil des Rohrlasers ist die Möglichkeit, bereits in der Schneidphase Bohrungen oder Durchbrüche in nahezu jeder gewünschten Form einzubringen. Dadurch entfallen zusätzliche Arbeitsschritte auf separaten Maschinen, was ebenfalls Zeit und Kosten spart.
Positionierhilfen und Verbindungselemente
Die Flexibilität des Rohrlasers erlaubt die Einbringung individueller Positionierhilfen. Diese reichen von einfachen Gravuren zur visuellen Unterstützung bei der Montage bis hin zu komplexen Bajonett- oder Puzzleverbindern, die Bauteile formschlüssig zusammenfügen. Derartige Verbindungen erleichtern nicht nur die Montage, sondern minimieren Fehlerquellen erheblich. Durch eine gezielte geometrische Gestaltung kann sichergestellt werden, dass Bauteile nur in der korrekten Ausrichtung zusammenpassen. Dies reduziert die Fehlerquote und steigert nicht zuletzt die Prozesssicherheit.
Zusätzlich können mithilfe der Rohrlasertechnik Identifikationsmerkmale wie Teilenummern, Fertigungsanweisungen oder Lagehinweise direkt auf die Bauteile graviert werden. Dies erleichtert die Weiterverarbeitung und sorgt für eine lückenlose Dokumentation im Fertigungsprozess.
Fazit: Effizienzsteigerung durch moderne Rohrlasertechnik
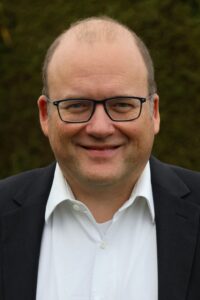
Der Einsatz von Rohrlasern in der Fertigung eröffnet zahlreiche neue Möglichkeiten zur wirtschaftlichen und präzisen Herstellung von Bauteilen. Entscheidend für eine maximale Effizienz ist jedoch die frühzeitige Berücksichtigung der Technologie bereits in der Konstruktionsphase. Unternehmen profitieren von einer engen Zusammenarbeit mit Fertigungspartnern, die über langjährige Erfahrung in der Rohrlaserbearbeitung verfügen. Die Kombination aus technologischem Know-how und optimierten Fertigungsprozessen sorgt für eine signifikante Reduktion von Produktionszeiten und Kosten – ein entscheidender Wettbewerbsvorteil für innovative Metallverarbeitung.
Kontakt: