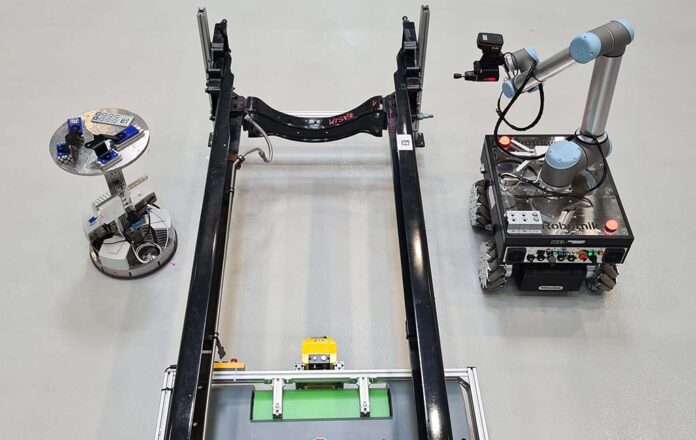
Eine mobile Roboterplattform ist eine vorteilhafte Kombination aus fahrerlosem Transportsystem (FTS) und Industrieroboter (IR), der meist sechs bzw. sieben Achsen aufweist. Als Verknüpfung von Transportflexibilität des fahrerlosen Transportsystems und Handhabungsflexibilität des Industrieroboters erlaubt sie die effiziente Durchführung anspruchsvoller Montageaufgaben an beliebigen Positionen auf dem Shopfloor der Produktion.
Relevante Handhabungs- und Montageaufgaben betreffen hierbei bspw. das Fügen von Bauteilen zu Baugruppen durch Kleben, Schweißen oder Schrauben. Diese Vorteile nutzen die XL Assembly GmbH und das Werkzeugmaschinenlabor WZL der RWTH Aachen bei der gemeinsamen Realisierung eines mobilen Schraubprozesses für eine Anwendung im LKW-Rahmenbau.
Kundenindividuelle Anforderungen, die zunehmende Volatilität an den Absatzmärkten sowie komplexe globale Entwicklungen infolge von (über-) regionalen Konflikten, Klima- und Gesundheitseinflüssen stellen nur einige der wettbewerbsentscheidenden Faktoren des Produktionsgeschehens dar.
Daher sollte sich die Montage der Zukunft auf die resiliente Erzeugung individualisierter Produkte ausrichten. In diesem Kontext arbeiten die XL Assembly GmbH und der Lehrstuhl für Fertigungsmesstechnik und Qualitätsmanagement des WZL der RWTH Aachen gemeinsam an flexiblen und mobilen, roboterbasierten Montagelösungen.
Sogenannte „Linienlose Mobile Montagesysteme“ (engl. „Line-less Mobile Assembly Systems“) liefern dabei den organisatorischen Rahmen der notwendigen Produktions- und Leitsysteme und bieten zeitgleich eine maximale Flexibilität und Resilienz. Dass sich zukünftig alle benötigten Ressourcen, wie die mobile Roboterplattform und fahrerlose Transportsysteme, frei und autonom in der Fabrik bewegen und somit temporäre Arbeitsstationen schaffen, ist die Vision der Forscherinnen und Forscher.
Je nach Auftragslage reorganisieren sich diese in Echtzeit zur Durchführung von angepassten Prozessen. Der Montageablauf erfolgt dadurch nicht mehr entlang von starren Linien, sondern entlang optimaler und auftragsindividueller Jobrouten zwischen ortsveränderlichen Montagestationen. Die Vernetzung aller eingesetzten Ressourcen stellt dabei die notwendigen Informationen für digitale Zwillinge der Produktionssysteme bereit.
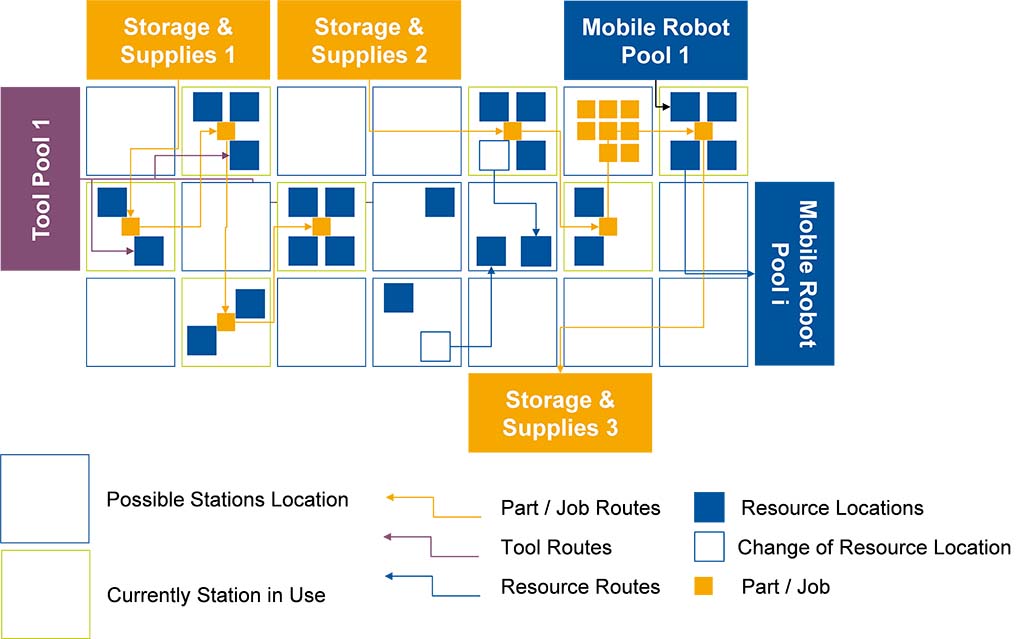
Mobile Roboter zur Durchführung von Schrauboperationen im LKW-Rahmenbau
Exemplarisch wurde eine räumlich-örtlich flexible Montagestation für Schraubprozesse für den LKW-Rahmenbau realisiert. Auf einer möglichst hindernisfreien Arbeitsfläche, basierend auf dem so genannten „Clean Shopfloor Approach“, wird der LKW-Rahmen auf einem Werkstückträger mittels fahrerlosem Transportsystem bereitgestellt.
Anschließend erkunden mobile Robotereinheiten die räumlichen Restriktionen mittels „Simultaneous Location and Mapping“ und erzeugen somit eine Karte der Umgebung. Auf dieser Basis bringen die mobilen Roboterplattformen schließlich die benötigten Schrauben zur Montageposition am Rahmen.
Die Einheiten sind dazu mit geeigneten Magazinen ausgestattet. Weiter kommt ein Schrauber als Werkzeug am Handgelenk des Industrieroboters der Plattformen zum Einsatz, zusätzlich ist eine Kamera montiert. Am LKW-Rahmen angekommen, ist die Lage der Baugruppe relativ zu der mobilen Roboterplattform zu identifizieren.
Es erfolgt eine Referenzbewegung des Industrieroboters, um mittels Kamera marker- oder punktwolkenbasiert die Lage der Baugruppe im Roboterkoordinatensystem festzulegen. Dynamisch, wird in diesem Koordinatensystem eine kollisionsfreie Bewegung des Industrieroboters geplant, um den drehmomentgesteuerten Schraubprozess durchzuführen.
Die Überwachung des Prozesses erfolgt über ein Leitsystem, das die Zustände aller angebundenen Einheiten konsolidiert und den Mitarbeiterinnen und Mitarbeitern zur Verfügung stellen.
Diese und weitere Lösungen werden am Center der XL Assembly GmbH konsortial mit dem WZL der RWTH Aachen erarbeitet, um sie anschließend in bilateralen Projekten an spezifische Montageanwendungen anzupassen und flexible roboterbasierte Anlagen für Feld und Praxis zu realisieren.
Kontakt: