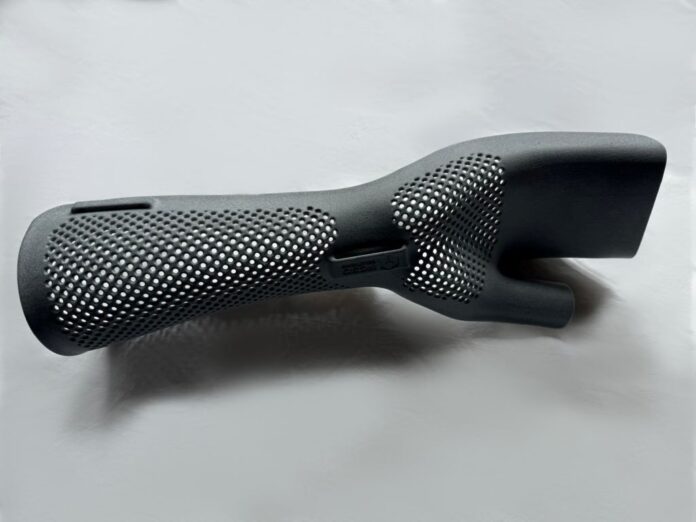
Individuell gefertigte orthopädische Armschienen sind eines der vielen 3D-Druckerzeugnisse der IFC Intelligent Feeding Components GmbH, das eine jederzeit verlässliche Oberflächenqualität mit hohem Tragekomfort voraussetzt. Um dies zu gewährleisten, kommt seit einiger Zeit eine S1 Anlage von AM Solutions – 3D post processing technology zum Einsatz – mit hervorragenden Ergebnissen.
Die IFC Intelligent Feeding Components GmbH aus dem baden-württembergischen Oedheim ist nicht nur Experte für innovative Zuführ- und Montagetechnik, sondern verfügt auch über ein modernes 3D-Druckzentrum. Dort werden hochwertige 3D-Druckerzeugnisse für verschiedenste Branchen in Kunststoff und Metall gefertigt und häufig sogar speziell für die Kunden mittels innovativer 3D-Scans konstruiert. Hierzu zählen unter anderem orthopädische Armlageschienen, die von eigenen Orthopädietechnikern im Haus individuell designt und angepasst werden.
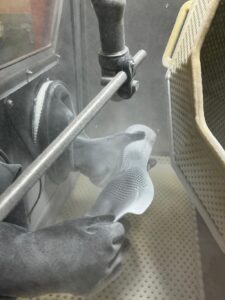
Um langfristig eine gleichbleibend hohe Oberflächenqualität und Reproduzierbarkeit zu gewährleisten, entschied sich das Unternehmen, in eine Post Processing Lösung zu investieren. „Wir haben vieles ausprobiert und sind dann auf der Formnext 2022 mit AM Solutions ins Gespräch gekommen“, erzählt Dominik Riegg, Leiter Additive Manufacturing bei IFC Intelligent Feeding Components GmbH. „Uns ist gleich positiv aufgefallen, dass die komplett inhouse hergestellten Anlagen sehr robust sind und somit auch rauen Industrieansprüchen gerecht werden. Zudem wurde sehr schnell verstanden, welche Anforderungen wir haben und uns mit der S1 eine optimale Lösung präsentiert.“
Polybeads vs. Glasperle
Im 400 m2 großen Customer Experience Center von AM Solutions – 3D post processing technology in Untermerzbach konnten die Verantwortlichen der IFC schließlich die Anlage vorab testen und sich über die verschiedenen Strahlmittel informieren. „Wir haben uns für das Strahlen mit Polybeads entschieden. Sie sind in der Anschaffung zwar teurer, aber deutlich langlebiger als Glasperlen“, führt Riegg aus. Ein weiterer Vorteil ist, dass die Oberfläche eine schönere Farbe sowie eine samtige Haptik aufweist. „Die Glasperlen haben sich in die Oberfläche eingeschossen, was gerade im medizinischen Bereich problematisch ist. Dank der Polybeads erhalten wir eine glatte und absolut homogene Oberfläche, die ein angenehmes Tragen der Armschiene ermöglicht.“
70 Prozent Zeitersparnis
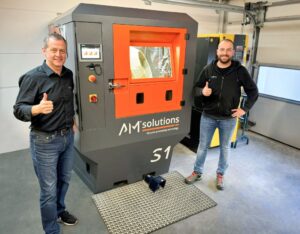
Vor der Anschaffung der S1 musste IFC die 3D-Druckerzeugnisse erst händisch auspacken und dann manuell strahlen. Nun kommen sie nach dem Entpacken direkt in die Strahlanlage, die sowohl die Reinigung als auch das Oberflächenfinish als 2-in-1 Lösung in einem Schritt mit nur einem Medium abbildet. Durch die gleichmäßige Rotation der Werkstücke beim Bearbeitungsprozess gewährleistet sie ein oberflächenschonendes und stets reproduzierbares Strahlergebnis. „Beim manuellen Strahlen war die Qualität immer unterschiedlich. Nun haben wir die Sicherheit, dass alles passt und gleichzeitig sparen wir uns bis zu 70 Prozent an Manpower“, erklärt Riegg.
Tatsächlich schafft die S1 etwa doppelt so viele Armschienen im Gegensatz zur manuellen Bearbeitung und die Zeit, in der die Maschine läuft, kann vom Personal für andere Tätigkeiten genutzt werden. „Heute denken wir zunehmend in Kleinserien“, führt Riegg aus, „damit wir hier wirtschaftlich bleiben, müssen wir immer mehr automatisieren und uns dabei auf 100-prozentige Prozesssicherheit verlassen können. Das Post Processing ist ein wesentlicher Faktor, der weit über das reine Hübschmachen eines Produkts hinausgeht. Am Ende ist es entscheidend für die gleichbleibende Qualität sowie Reproduzierbarkeit und erweitert die Grenzen des Machbaren. Unsere Investition in die S1 hat sich bereits in 1,5 Jahren amortisiert, aber vom Nutzen profitieren wir langfristig.“
Kontakt: