„Wir haben eine Fertigungszelle entwickelt, die es ermöglicht, komplexe Implantate
schnell, zuverlässig und mit hoher Qualität zu produzieren und dies unter
Berücksichtigung der wichtigen regulatorischen Anforderungen, wie die seit 2019 in
Kraft getretene neue europäische Medical Device Regulations (MDR)“, erläutert Sebastian Kaiser vom Institut für Fertigungstechnik und Werkzeugmaschinen (IFW) der Leibniz Universität Hannover.
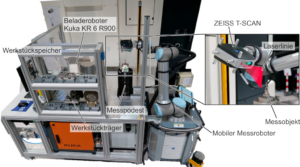
Nach über drei Jahren Forschungsarbeit und in enger Zusammenarbeit mit fünf
Industrieunternehmen hat das IFW das vom Bundesministerium für Bildung und Forschung
geförderte Projekt „Teilautonome Fertigungszelle für orthopädische Implantate“ (TempoPlant)
erfolgreich abgeschlossen. Die Ergebnisse sind so vielversprechend, dass nun der Transfer in
industrielle Praxis nahtlos anschließen kann. Kaiser: „Die neue MDR ist für die Unternehmen der Medizintechnik eine große Herausforderung. Mit der teilautonomen Fertigungszelle ermöglichen wir den Unternehmen einen wirtschaftlichen Fertigungsprozess.“
Schwer zerspanbare Werkstoffe, komplexe Geometrien und geringe Stückzahlen zeichnen die
Fertigung von Implantaten aus und sind eine große Herausforderung für die produzierenden
Unternehmen. Daneben ist ein enormer Aufwand zur medizintechnischen Zulassung der
Fertigungsprozesse notwendig, bevor ein Produkt eine Marktzulassung erhält. Die Unternehmen der Medizintechnik bewerten die gestiegenen Anforderungen durch die MDR als größtes Hemmnis in der Unternehmensentwicklung, da mit großem Aufwand eine umfassende Dokumentation erstellt werden muss.
Unternehmen investieren inzwischen etwa 9 Prozent des Gesamtumsatzes in die Erfüllung der MDR. Die gestiegenen Anforderungen und Kosten führen bereits jetzt dazu, dass Implantate mit geringen Stückzahlen aus Kostengründen vom Markt verdrängt werden. Projektmitarbeiter Sebastian Kaiser: „Das kann im schlimmsten Fall auch mit einer Gefährdung der Patienten verbunden sein, wenn notwendige Implantate nicht mehr verfügbar sind.“
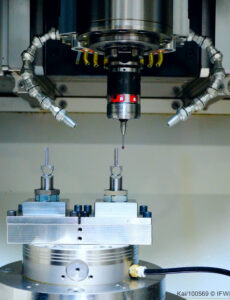
Für die Herstellung der Implantate erforschten die Projektmitarbeitenden Methoden der
Digitalisierung sowie innovative Fertigungstechnik und wendeten sie entlang der gesamten
Prozesskette an. Die Digitalisierung beginnt beim Einsatz von Produkt- und Fertigungsinformationen (PMI). Technische Zeichnungen in der Arbeitsvorbereitung sind dadurch nicht mehr erforderlich. Neben der Planung wurde ebenfalls der Fertigungsprozess automatisiert. Ein Automatisierungsroboter übernimmt das Bauteilhandling. Parallel zum Fertigungsprozess läuft eine Prozessüberwachung, die Fehler in Echtzeit erkennt und darauf reagieren kann.
Unmittelbar nach dem Fertigungsprozess wird eine automatisierte Qualitätskontrolle mit einem Messsystem in der Werkzeugmaschine und einem optischen Messsystem der am Projekt beteiligten Firma ZEISS Optotechnik GmbH ausgeführt. Das Optische Messsystem wird dafür von einem Messroboter geführt. Die ausgewerteten Messdaten werden zur Optimierung des Fertigungsprozesses verwendet.
Neben der Dokumentation spielt die Validierung der Fertigungszelle eine wichtige Rolle. Für die
Unternehmen der Medizintechnik stellt sich dabei immer wieder die Frage, wie ein Prozess validiert werden kann, der mit Hilfe der Fehlerkompensation selbständig Veränderungen an den Werkzeugwegen vornimmt. In diesem Fall liegt der Schlüssel in dem Einsatz der genannten Messsysteme. Durch die lückenlose Qualitätskontrolle kann eine Verifizierung der kompensierten Flächen durchgeführt werden. Das erleichtert die Validierung der Fertigungszelle enorm, da durch die Verifizierung ständig ein Nachweis über die korrekte Funktionsfähigkeit der Fertigungszelle erbracht wird.
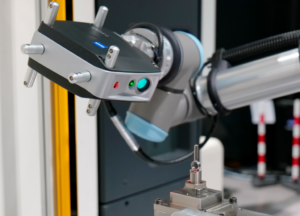
Insgesamt wurden verschiedene Technologien in eine gemeinsame Fertigungszelle integriert und erfolgreich erprobt. Nach dem erfolgreichen Abschluss des Projekts arbeitet das Projektteam mit seinen Industriepartnern DECKEL MAHO Seebach, DMG MORI Digital, Carl Zeiss Optotechnik GmbH, endocon GmbH und der MACK Dentaltechnik GmbH im nächsten Schritt an einer Industrialisierung der Technologien.
Kontakt: